How do you manage rising injury rates in a growing industry which employs more than 6000 people, with no industry body representation and no clearly recognised safety training programs that teach consistent safety standards and where workers are twice as likely to have a serious injury?
The formwork industry is one of the largest employers in the building industry and along with its high risk nature possesses one of the lowest safety records in the construction industry.
These are the issues that a leading group of formwork contractors is currently tackling head on, with an overarching aim of improving safety standards in the Australian formwork industry.
In August, a draft code of practice on how to manage risks in the formwork and falsework industry in New South Wales was released.
According to SafeWork NSW Executive Director Tony Williams, more than 6000 people work in the concrete construction services industry, and formwork construction puts these workers in high-risk situations, such as being exposed to the risk of falls from heights, being struck by falling objects and muscular stress.
“…so it is vital that businesses are applying consistent safety standards,” Mr Williams said.
The draft code outlines the incident prevention measures and ongoing risk assessment that workplaces should adopt in order to avoid these risks.
“Falls from heights are a major cause of fatalities and serious injuries in the construction industry in NSW. Most people who are seriously injured of killed, fall from a height of four metres or less,” Mr Williams said.
“Some of the major injuries sustained while working from a height happen as a result of falling from a ladder or noncompliant scaffolds, both of which are positions formwork tradesmen may find themselves in,” Mr Williams said.
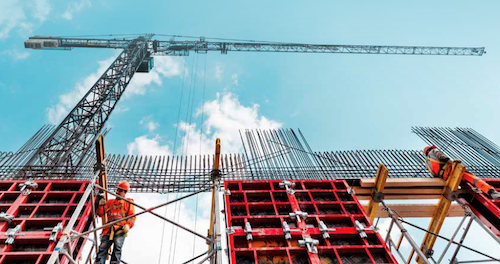
DELVING INTO THE SAFETY ISSUES IN THE SECTOR
Two years ago, a group consisting of SafeWork NSW, the Master Builders Association, CFMEU, and construction and formwork companies embarked on a journey to discuss and revise the 1998 Formwork Code of practice.
It was clear that the interests of formworkers in Australia were not supported, and this in combination with increasing injury figures, meant the safety of formworkers in Australia needed to be urgently addressed and reviewed.
As a result, some of the formwork companies’ business owners got together and sought expert knowledge in establishing an industry body and conducted a number of strategy workshops to ensure the future sustainability of the association as an inclusive network of formworkers and those with an interest in or associated with the industry.
This led to the establishment of the Formwork Industry Association (FIA) in 2018. The association is supported by members, formwork contractors, a number of the leading construction companies, companies associated with the formwork industry and SafeWork NSW.
The formwork industry has never had a trade association that represents their interests before, mainly because it has been difficult or impossible for any single company, no matter how large, to singlehandedly undertake the interests of the industry.
Since its establishment, the FIA has obtained a significant amount of positive industry support from all segments of the building industry, all in favour of supporting the FIA and working together to improve the safety standards in the industry.
LACK OF TRAINING AND LABOUR DEMAND
The FIA has recognised that there are multiple safety issues in the formwork industry, including the lack of industry safety awareness, lack of identified skilled labour, lack of consistent training of workers, unavailable support to contractors on industry issues and no complying or regulating industry body within the sector other than Safe Work Australia. Safe Work Australia provides the industry with formwork and falsework guidance material and is responsible for the Code of Practice, but there is a different Code in each state, all of which have different definitions.
These factors, in combination, have resulted in an industry that attracts numerous untrustworthy contractors and workers, which has led to the discrediting of the formwork industry as a whole while contributing to the building industry’s worst reputation when it comes to safety records.
A person who erects, alters or dismantles formwork and falsework must be competent to do the work safely, but according to the FIA, it is currently impossible to ensure that workers are both trained and competent to perform work safely in line with the revised Code of Practice in NSW.
This is because there is a lack of accessible and specific formwork training programs with certification and verification of competencies outside the Certificate III qualification.
Tickets used to verify the competency of a worker, but since their removal it has become impossible to confirm whether a worker can do the job.
“With the removal of tickets, any worker can arrive on site and state they are a formworker,” the FIA says.
Although a person which undertakes construction work must have successfully completed general construction induction training, the increasing demand for labour and pressures on formwork contractors to complete the work means competencies are sometimes not established until the worker arrives on site.
IMPROVING THE INDUSTRY
The FIA’s main aim is to improve safety within the industry, first by reviewing the Code of Practice for NSW to ensure it is in line with Australian standards, secondly by ensuring clarity on procedures to guarantee the Code is clear for all workers, and thirdly, the FIA will look at a Code that is consistent across all states.
The FIA also looks at existing training and competencies to ensure that it is accessible and affordable for all workers and tiers of contractors. The aim is for the training to comprise of short, accessible and relevant courses that can be performed on site or at a suitable training venue. It should also provide a certification that can be recognised by the construction industry.
The FIA also plans to perform assessment on verification of competencies to ensure that experienced and seasoned workers are assessed regularly, and if required are provided with training.
Finally, the FIA works to attract future workers by demonstrating the opportunities within the industry, and providing awareness, education and career paths for future workers.
ABOUT THE FORMWORK INDUSTRY ASSOCIATION
As Australia’s first industry body for formworkers, the FIA is committed to growing members’ credibility, connections,recognition and safety knowledge.
The FIA strives to continuously improve competence and safety across the industry by bringing the stakeholders together for networking, advocacy and knowledge sharing to raise standards and minimise risk.
As an FIA member, companies show they are serious about worker safety and the safety within the industry.
It also demonstrates a commitment, formwork expertise and ethical standards to future employees, clients and principal contractors. It further establishes an organisation’s commitment to continually building its own and workers’ safety expertise and professional network.
The FIA believes in sharing formwork and safety knowledge. As such, the association has created a ‘knowledge channel’ for members to access the latest safety videos, articles and important documents to make sure members and their workers are a step ahead of the rest.
Members get access to a series of events and a monthly newsletter which includes best practice and developments in the marketplace. The FIA’s partner program is also a vital part in sharing this information to members and improving access to the best safety knowledge.
Article sourced from Michael Sugg GM Formwork Industry Association and featured in the October 2019 Issue of Build Australia Magazine.